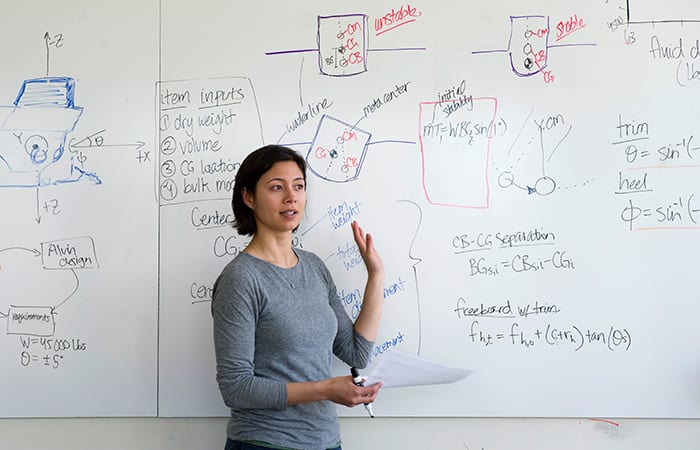
Rebuilding Alvin: Kakani Katija Young
A series on the people who reassembled the iconic sub
From the beginning of 2011 to May 2013, Alvin, the U.S. science community’s only human-occupied submersible dedicated to deep-sea research, underwent a thorough overhaul and upgrade to greatly enhance its capabilities. In the end, the iconic sub was redesigned and rebuilt, piece by piece, by a one-of-a-kind team of engineers, technicians, and pilots at WHOI.
Here, WHOI postdoctoral scientist Kakani Katija Young talks about using math and physics to solve an engineering problem: calculating the sub’s weight and stability.
In designing Alvin, the sub has to meet basic requirements to function and to ensure it’ll come back when you put it in the water. It has to be buoyant in the water, not weigh too much, and to balance—not tip up, down, or to the side.
There are some 450 components that went into the new Alvin—many of them never used before. Based on the weight, buoyancy, and position in the sub of all the components, we can figure out the vehicle’s buoyancy, center of gravity, and stability.
I came here as a postdoctoral scholar, studying the fluid dynamics of swimming jellyfish, but my undergraduate degree was in aerospace engineering. I had done systems engineering on spacecraft design projects, including the International Space Station, at NASA Ames Research Center. Loral O’Hara, an engineer on the Alvin project, is also an aerospace engineer and was aware of what I had done, and I was brought into the project to conduct weight and stability analyses for Alvin.
As the design progressed, engineers gave me information on the weight, volume, compressibility, and exact position of each part. Using these and engineering equations, I wrote algorithms—using a commercial computer program called Matlab—that informed us, at each stage in the design, what the sub looked like in terms of weight and buoyancy, and whether we needed to redesign or rearrange placements of items on the vehicle to meet weight and stability requirements. Another challenge was that, because seawater density and pressure increase with depth, the sub’s buoyancy also changes with depth.
This is systems engineering. You’re taking information from different subsystems, compiling it, and figuring out if the sub is stable in a variety of operating conditions. With the algorithm I developed, I predicted trim—how far you pitch forward or backward—and heel—how far you pitch to one side or another. And I calculated freeboard, the distance from the water line to the top of the sail. That’s important, because the air intake is on the sail; if the intake is below the water line, you’re in trouble.
In April, we weighed the vehicle. We predicted it to weight 29,541 pounds, and the weight was 29, 690—only 150 pounds different! A very small percent of the total, so we were pleased. Then we measured the free lift angle—how much it pitched up when you lift it—at 2.5 degrees. Based on the code, we had predicted 2.1 degrees—the measurement was really close! We were celebrating when that happened, because the code accurately predicted what we found. So we could trust the computer program and use it effectively to guide design and construction of Alvin, and for future vehicles.
These equations aren’t new. They’ve been used for marine engineering, gosh, ever since we started designing boats. They’re based on mass, weight, buoyancy, and a lot of geometry, calculating what happens to the center of gravity as you change the design.
You know, you always assume that physics and math work. But to have gone through this rather complicated stuff, using geometry and physics, and predict a number, and then to have it be extremely close, was almost a revelation. It affirms your faith in science and math.
Alvin is owned by the U.S. Navy and operated by WHOI. The current upgrade has been funded largely by the National Science Foundation, with support from private donations to WHOI.