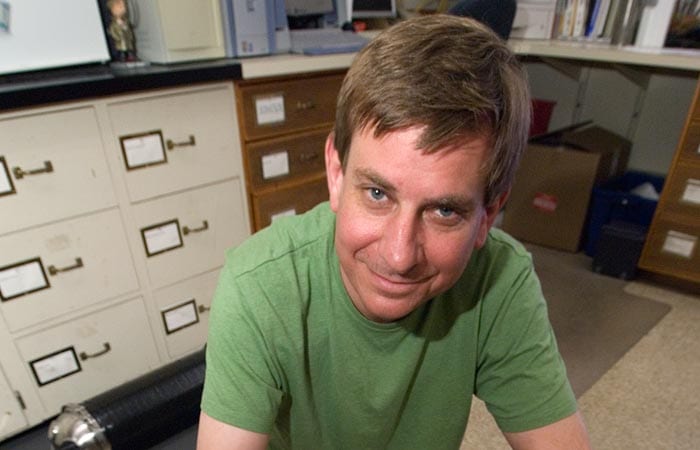
Floating Without Imploding
A conversation with WHOI engineer Don Peters
To allow a heavy vehicle to float in the deepest depths, Don Peters and other engineers at Woods Hole Oceanographic Institution used an entirely new system of ceramic spheres that would provide lift and, at the same time, would not implode under pressures reaching 16,500 pound per square inch.
[Fifth in a series of interviews with five WHOI engineers who developed the new deep-sea exploration vehicle Nereus, which successfully dove to Challenger Deep, the deepest part of the ocean, on May 31, 2009.]Oceanus: Let’s start with a “dumb” question that may not be obvious to readers: Why do you need flotation on the Nereus vehicle?
Peters: Well, most of the things that make up a vehicle are heavy in water: its aluminum structure, battery packs, cameras, lights. If you just put that stuff in there without any flotation, the vehicle would sink to the bottom, and you wouldn’t get it back. Flotation provides the necessary buoyancy to make the vehicle neutral, as they say, which means it won’t float up or sink down. Of course, if you’re going deep, that flotation material has to be strong enough to withstand the pressure to which it will be exposed.
Oceanus: In previous deep-sea vehicles, engineers traditionally have used a pressure-resistant material called syntactic foam to provide flotation. What is that, and why didn’t you use it for Nereus?
Peters: Syntactic foam is made up of small balloons of glass, mixed with epoxy into a matrix and formed into blocks. The glass microspheres are capable of withstanding pressures up to about 10,000 psi, or depths of about 6,000 meters. That represents 95 percent of the ocean, so not a lot of syntactic foam is made to survive deeper than that. To make syntactic foam that could go deeper would have taken quite a bit of research and development. It probably could be done, but it seemed like an expensive and time-consuming path to go on.
Oceanus: How did you think of using ceramic materials instead?
Peters: We were using ceramic for pressure housings [pressure-resistant compartments enclosing vehicle components]. Ceramics, when compressed, have about fives times the strength of steel, but weigh about a third as much. They are a relatively inexpensive raw material. It is a widely used engineering material, whose behavior is well understood.
In looking at the options, we were aware of a fellow named Jerry Stachiw, who had done by far the most experimental work developing ceramic pressure housings for the Navy in the 1970s and ‘80s. I looked him up and found he was in business in Texas and gave him a call. We hired Jerry and his wife Joan as consultants. It turned out that he had also been looking into making seamless ceramic spheres for flotation. We listened to what they had to say, and they were a tremendous asset to the project. Unfortunately, Jerry died unexpectedly in April 2007, right before we started sea trials off Hawaii to test the ceramic spheres on Nereus.
Oceanus: How did you figure out the right size for the spheres?
Peters: Initially we at looked at making the biggest possible spheres, thinking that would minimize the pain associated with manufacturing and testing them. We originally made a number of experimental 10-inch spheres, but then we became aware that a company called DeepSea Power & Light had already done a lot of work testing and verifying 3½-inch ceramic spheres for a use in the oil-production industry. We became convinced that they had a real commitment to manufacturing these things in high volume at a good price, and we put in an order for 1,750 spheres, which gave them momentum to ramp up their production capability. DeepSea Power & Light did all the manufacturing, quality control, testing, and delivered a product that was ready to go in the water.
Oceanus: These spheres aren’t made of the same ceramics in the coffee mug I used this morning, right?
Peters: Your coffee cup is probably made of some kind of clay, but it certainly wasn’t fired to the same high temperatures as these spheres. They are made of pure aluminum oxide that, when heated to a high enough temperature, will melt together to form a real, uniform material with incredibly high compressive strength. It’s almost like making a diamond or something like that. It’s very strong when you push on it, but like something that’s made of glass, or like a coffee mug, it’s also very brittle and capable of breaking.
Oceanus: How can something so fragile also be so strong?
Peters: The magic is that the external pressure we’re putting the sphere under is completely uniform—from the water around it. The spheres are as circular in all directions as can be manufactured, and that geometry distributes the load uniformly in all directions along the skin of the sphere. So even though the spheres are about the thickness of a tortilla chip, about 50/1,000ths of an inch thick, they can handle a lot of compression.
Oceanus: Tell us a little about how the spheres are manufactured.
Peters: The ceramic powder is mixed with water. You pour the liquid into a mold with a spherical cavity, close it up, and put it in a machine that rolls the mold in all directions to generate a sphere with uniform wall thickness and no seams. After a few minutes, the sphere is hard enough to be taken out of the mold. Then spheres go through a series of drying and firing stages in high-temperature kilns. All the alumina powder granules fuse in such a way that the air in the middle cavity just outgases, and when the spheres cool down, you end up with a partial vacuum inside.
It turned out that the smaller spheres are easier to manufacture than the 10-inch spheres. They have thinner walls so they’re less prone to non-uniformities. And we found the 3½-inch spheres were much nicer to work with for packing inside Nereus’s hull.
Oceanus: How so?
Peters: One of the largest challenges was designing the matrix to pack the spheres efficiently into the vehicle’s hulls. It sounds kind of weird, but it occupied a number of years of my thinking trying to figure out how to jam as many of these things in there as possible. The bigger spheres left less margin to make them fit into an unusual hull shape.
Oceanus: Sort of like packing a box with Ping-Pong balls rather than with bowling balls—you can use more available space with Ping-Pong balls. How did you pack ‘em in?
Peters: We ended up cutting 1-inch-thick plastic sheets in what looks like slices of bread, and each slice has lots of holes in it to put in the spheres. We lined up all these slices so that the holes run right through the whole loaf. The arrangement allows us to pack about seven or eight hundred spheres in each hull. Each sphere provides a little over a half-pound of lift. And the plastic sheets, also being lighter than water, add a significant amount of buoyancy.
Oceanus: I assume the spheres undergo some fairly rigorous testing before you actually put them in.
Peters: In the manufacturing process, the spheres are cycled through pressure-testing chambers to verify that can take significantly greater pressures that they will have operate under. A technology called acoustic emission is used: You listen for very high-frequency sound waves, which are created from any kind of brittle fracturing or any sort of flaw in the sphere. If those signals come from the spheres, they are discarded. That being said, there’s still some small chance that one of these things might fail at depth.
Oceanus: So they resist pressure, but what would happen if you dropped one?
Peters: You probably don’t have to drop one much more than about a foot, and it’ll shatter like a Christmas tree ornament. But DeepSea Power & Light came up with a clear plastic jacket that goes over the spheres and protects them from damage if they are dropped, or if they bump into one another. The jackets also protect the sphere surface from getting scratched. At the factory, you could take a sphere with a jacket on and throw it again the concrete floor as hard as possible, and it’ll bounce, but it won’t break.
Oceanus: We heard a rumor that you were going to play softball with one of the spheres. Have you tried it?
Peters: [Laughs] Never tried it, no.
—Interview conducted by Amy E. Nevala and edited and condensed by Lonny Lippsett
Funding to develop Nereus was provided by the National Science Foundation, the Office of Naval Research, the National Oceanic and Atmospheric Administration, the Russell Family Foundation, and WHOI.
From the Series
Slideshow
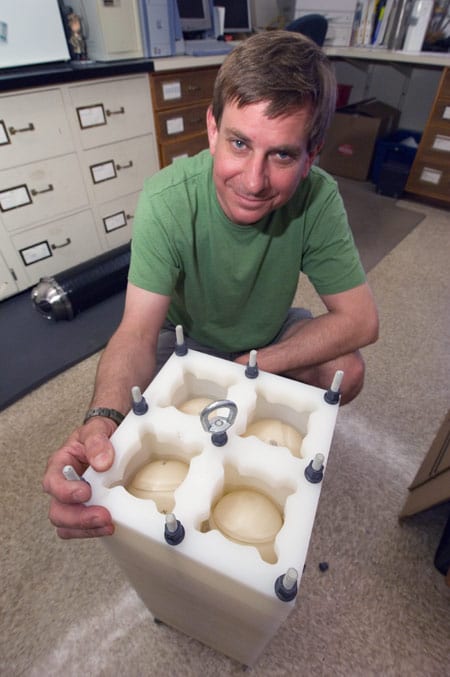
Slideshow
- Don Peters, an engineer at Woods Hole Oceanographic Institution, supervised the design and building of special ceramic spheres to provide buoyancy for the new Nereus deep-sea vehicle. Nearly 800 hollow spheres are packed into each of Nereus's two hulls allow it to float under water. (Photo by Tom Kleindinst, Woods Hole Oceanographic Institution)
- Each sphere is 3½ inches in diameter, with a skin about 50/1,000ths of an inch thick. They can withstand imploding under 16,500 pounds per square inch—the pressure 7 miles under the sea. (Photo by Tom Kleindinst, Woods Hole Oceanographic Institution)
Video
Related Articles
Featured Researchers
See Also
- Nereus Soars to the Ocean's Deepest Trench from Oceanus magazine
- Interview with Andy Bowen from Oceanus magazine
- Interview with Matt Heintz from Oceanus magazine
- Interview with Daniel Gomez-Ibanez from Oceanus magazine
- Interview with Jon Howland from Oceanus magazine
- DeepSea Power & Light Manufacturer of the ceramic flotation spheres for Nereus.
- National Deep Submergence Facility