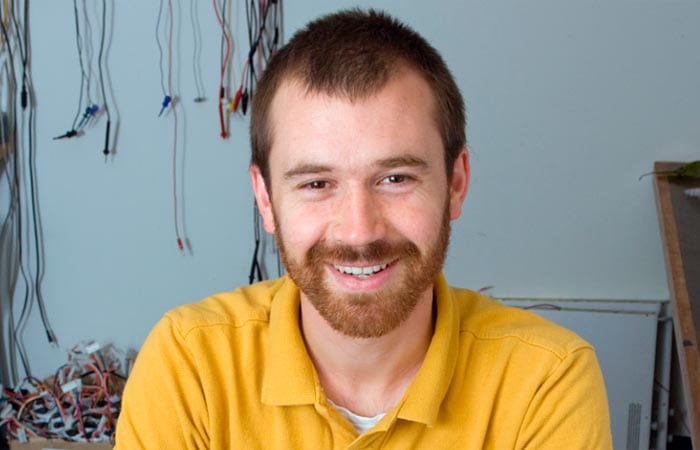
2,000 Batteries Under the Sea
A conversation with WHOI engineer Daniel Gomez-Ibanez
Daniel Gomez-Ibañez has been an engineer at Woods Hole Oceanographic Institution for three years. Much of that time, he has spent developing large batteries for underwater vehicles, including Nereus.
[Second in a series of interviews with five WHOI engineers who developed the new deep-sea exploration vehicle Nereus, which successfully dove to Challenger Deep, the deepest part of the ocean, on May 31, 2009.]Oceanus: Why are batteries so important for Nereus?
Gomez-Ibañez: Unlike other remotely operated vehicles, we don’t have an umbilical to the surface ship, so batteries are our main power supply for propulsion, lights, operating the manipulator arm, etc.
Oceanus: Did you have to come up with a whole new design for batteries for Nereus?
Gomez-Ibañez: I leveraged a lot of development that happened in previous vehicles. So the first thing I did was, I went around to everyone I could find that had worked with battery-powered underwater vehicles and asked, “What problems did you have? What worked well? What didn’t work? What would you do differently next time?” I mean, I was standing on the shoulders of some giants, and that got me most of the way toward a functioning battery. What remained was just tailoring that to Nereus.
Oceanus: What is unique or different about the batteries for Nereus?
Gomez-Ibañez: This is one of the larger battery packages we’ve ever put in a deep-sea vehicle. The power output we needed to operate Nereus is higher, so we had to deal with higher currents and voltages than we previously used.
We use small packs of rechargeable lithium-ion batteries similar to those that go into I-pods, or cell phones, and laptop computers. But in this case, we used about 2,000 battery cells, whereas your computer might have only four.
Oceanus: This may sound like a silly question, but instead of 2,000 little batteries, why not use one giant battery?
Gomez-Ibañez: That’s not out of the question. Large cells are often used in military vehicles or satellites. But one advantage of using a small, mass-produced cell is that there’s been a huge investment in the repeatability and quality control of the manufacturing process. A very large cell doesn’t have that track record of consistency, because it may be the first, second, or even a 100th cell that has been made, and it’s hard to be sure that it’s a good design. So we used a lot of small cells made in a large volume and plugged them into one big power cord to end up with a very much larger battery. It’s the size of the battery that brings unique challenges.
Oceanus: Such as?
Gomez-Ibañez: I think the biggest problem with large batteries is striking a balance between safety and reliability. There’s a lot of energy stored in the batteries, so if they do for some reason heat up and catch on fire, a lot of energy is released. It would make a very big fire and probably destroy the vehicle and could endanger the safety of everyone on the ship. It’s not good to have a fire when you’re in the middle of the ocean.
A lot of effort also went into making the battery able to be shipped safely and economically. There are rules on what you can ship and how you can ship it, and we’ve designed the battery in such a way that it can be shipped with minimal effort, minimal delay, and minimal expense—so that you can ship it without any special treatment and on a regular passenger plane.
And that means we built in a lot of protection features, so that faults are detected and the batteries can turn off safely in the event of either damage, or short-circuiting, or a heat source that might present a fire hazard. So, for example we put in temperature sensors that turn off the battery if it gets too hot. There are several layers of protection built in, so that the batteries don’t pose a danger either in operation or in transit, and in particular, we went through several rounds of testing that confirmed that the batteries could be used and shipped safely.
Oceanus: How did you test them?
Gomez-Ibañez: We had a long list of possible failure modes of the batteries, and we tested each of the protection mechanisms we put in to prevent them. It doesn’t do any good to build something in, if you don’t know that it it’s going to work. So, for example, I used a heat gun to put some heat into the battery pack, and just observed its response—which, by the way, is that it will stop, whether the battery is discharging or charging.
Oceanus: Were there any hitches during the process?
Gomez-Ibañez: A few problems and unique issues come up when you increase the voltage beyond what you’d see in a laptop computer. So, fuses blow. Things burn up. Bad things happen. We just had to work through the problems and find the configurations that would be safe and work reliably.
Oceanus: Any major problems?
Gomez-Ibañez: Yeah, we definitely had a few of those, a few moments of panic along the development of batteries. Maybe the most memorable was, we worked through all the problems getting our battery pack assembled with the appropriate protection, and we had our prototype we were all happy with. We had 30 of them that were passing all our tests. So we had our assembler assemble the full complement of 300 batteries for the vehicle.
We started testing them, and we found they were overheating. There was a problem in there. We didn’t know what it was. So we started tearing battery packs apart and measuring temperatures and voltages all over the place, and we traced it down to a single transistor that is supposed to be able to switch the current on and off. But it had an unexpectedly high resistance.
It turned out that a “pirate” organization produced these parts, put some other manufacturer’s name on them, and sold them as legitimate parts. Once we had located this defective part, we sent it to the manufacturers that were supposed to have made it, and they said, “That’s not ours. We didn’t make it. It’s a counterfeit.” We had to redo those battery packs and essentially build them all over again with the actual transistor.
Oceanus: How much time did that cost you?
Gomez-Ibañez: It took probably two weeks to get to the bottom of the problem and then another three months to do everything over again.
—Interview conducted by Amy E. Nevala and edited and condensed by Lonny Lippsett
Funding to develop Nereus was provided by the National Science Foundation, the Office of Naval Research, the National Oceanic and Atmospheric Administration, the Russell Family Foundation, and WHOI.
From the Series
Slideshow
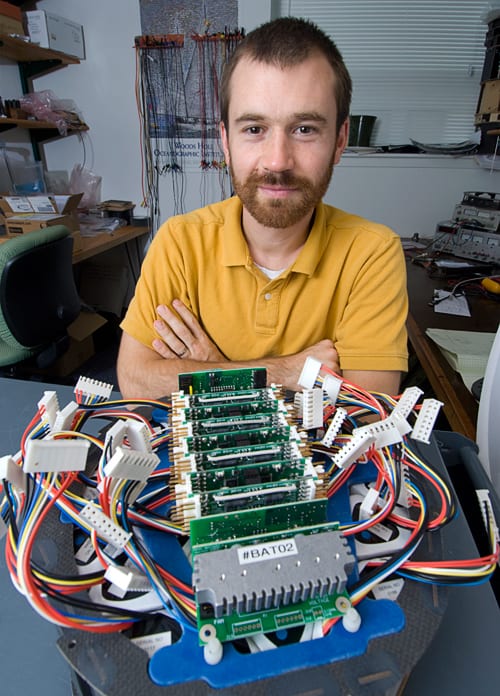
Slideshow
- Daniel Gomez-Ibañez is an engineer at Woods Hole Oceanographic Institution who specializes in developing battery systems to power deep-submergence vehicles, including the new "hybrid" deep-sea explorer, Nereus. (Photo by Tom Kleindinst, Woods Hole Oceanographic Institution)
- The new deep-diving robot Nereus is tested at sea. (Photo by Robert Elder, Woods Hole Oceanographic Institution)
Video
Related Articles
Featured Researchers
See Also
- Nereus Soars to the Ocean's Deepest Trench from Oceanus magazine
- Interview with Andy Bowen from Oceanus magazine
- Interview with Matt Heintz from Oceanus magazine
- Hybrid Remotely Operated Vehicle Nereus Reaches the Deepest Part of the Ocean WHOI News Release
- National Deep Submergence Facility