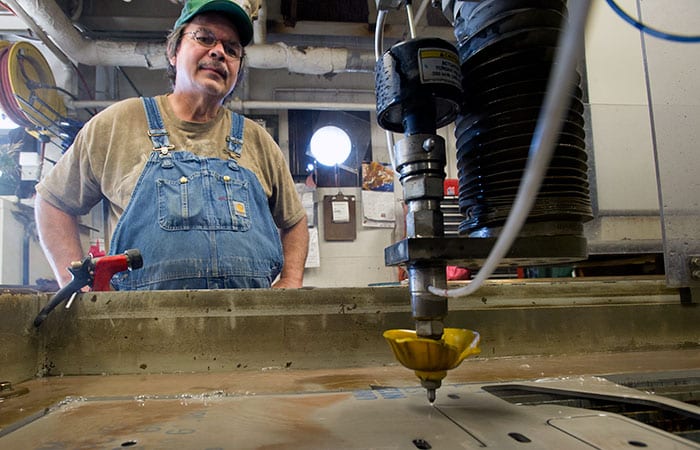
Rebuilding Alvin: Timothy Kling
A series on the people reassembling the iconic sub
Since the beginning of 2011, Alvin, the U.S. science community’s only human-occupied submersible dedicated to deep-sea research, has been undergoing a thorough overhaul and upgrade that will enhance its capabilities. The improvements include a new personnel sphere, updated command-and-control systems, enhanced lighting and high-definition imaging systems, new syntactic foam to provide buoyancy, and more and larger viewports, or windows.
The centerpiece is a larger personnel sphere with improved interior design to enhance the comfort of pilots and researchers who will occupy it. The titanium sphere is also designed to withstand pressure at depths of 6.5 kilometers (4 miles), with the eventual goal of allowing Alvin to dive beyond its current 4.5-kilometer (2.8-mile) diving capacity.
Now in the final stages of the first phase of the upgrade, the iconic sub is being painstakingly reassembled, piece by piece, by a one-of-a-kind team of engineers, technicians, and pilots at Woods Hole Oceanographic Institution (WHOI). They also carefully inspect and test each component to ensure its reliability and the safety of those who will use to sub to explore the depths.
Here, Timothy Kling talks about the water jet machine use to precisely cut pieces for Alvin.
This was titanium I was cutting, part of a frame piece on the Alvin. Almost every part for the sub starts out here. Everything that gets welded or machined I usually start, and then it goes to the welders or machine shop after I cut out the parts.
The water jet machine cuts with garnet, a semiprecious stone ground to 80 grit, particles of about 175 micrometers. It runs on 55,000 pounds per square inch of water pressure. The pressure and suction of the water going through the nozzle sucks the garnet through that hose, mixes it in a chamber, and then shoots it down through the material you’re cutting. Basically anything you stick underneath there, it’ll slice it right up, just like butter, from 1/32 of an inch of material up to eight inches of metal.
I’ll tell you what, it eats the material, it doesn’t really cut it. It’s taking material away from the piece. Then the garnet grit goes down to the bottom of the tank—it’s just mud. This weekend we’re going to take the whole machine apart and get in there and dig it out, because it’s full of garnet. A full day’s work.
The machine uses a computer program: I path it out, it comes up on the monitor, and you can see lines where it’s cutting. As the machine cuts, it follows the lines on the program.
It’s very precise. It has a tolerance of two-thousandths of an inch [on the cut line]. A human hair is three-thousandths.
You really gotta know your materials—a lot of time I stand right by the machine because of the type of material it is; other times I can walk away while it runs, and I’ve had programs that take nine hours. I do, sometimes, upwards of 60 to 80 parts in a day. The last month I’ve been working ten-hour days, six days a week, trying to keep up.
All that over there is Alvin material: One-inch stainless steel, one-inch Delrin plastic, here’s three-sixteenths-inch titanium, three-sixteenths urethane. When I use something, I have to write down what I’m doing, what kind of part, how much I used, and how much is left over. You’ve got to make sure you’re doing it the right way—with Alvin, you’re dealing with somebody’s life.
My grandfather and uncle were machinists and welders. I started out machining and welding in my grandfather’s garage when I was ten. Ah, it was great! I grew up in that garage.
I got an electronics degree, worked for my Dad’s vending business for years, got a degree in machining and welding, and I’ve done that ever since. I put in an application here as a machinist and Bob McCabe hired me in 2007. I’ve spent about two years with the water jet. It’s a machine I really enjoy running. I can pretty much build just about anything—it’s what I like to do.
Like my grandfather taught me from a young age, ‘Keep that tolerance.’ That’s the biggest thing for machining.
Alvin is owned by the U.S. Navy and operated by WHOI. The current upgrade has been funded largely by the National Science Foundation, with support from private donations to WHOI.
From the Series
Related Articles
- The story of a “champion” submersible
- Robots to the Rescue
- Who is Alvin and what are sea trials?
- 7 Places and Things Alvin Can Explore Now
- The story of “Little Alvin” and the lost H-bomb
- Meet the Alvin 6500 Team: Lisa Smith
- Overhaul to take Alvin to greater extremes
- Meet the Alvin 6500 Team: Rose Wall
- Racing an undersea volcano
Featured Researchers
See Also
- Building the Next-Generation Alvin from Oceanus magazine
- Alvin Gets an Interior Re-design from Oceanus magazine
- New Personnel Sphere Passes Pressure Test WHOI News Release
- Human Occupied Vehicle Alvin
- Alvin's Pilots from Oceanus magazine
- National Deep Submergence Facility