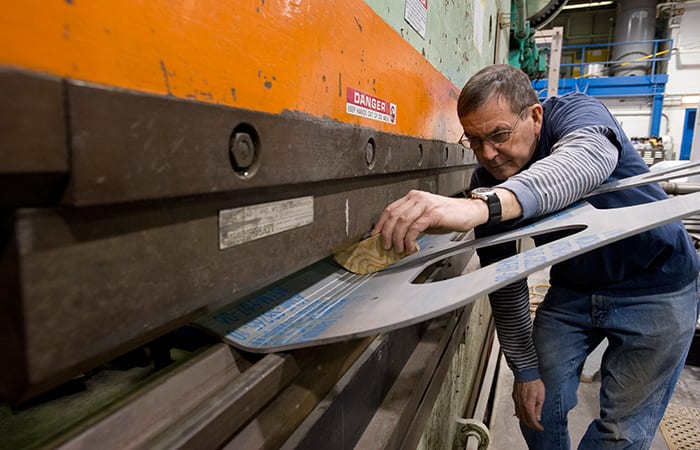
Rebuilding Alvin: Paul Keith
A series on the people who reassembled the iconic sub
From the beginning of 2011 to May 2013, Alvin, the U.S. science community’s only human-occupied submersible dedicated to deep-sea research, underwent a thorough overhaul and upgrade to greatly enhance its capabilities. In the end, the iconic sub was redesigned and rebuilt, piece by piece, by a one-of-a-kind team of engineers, technicians, and pilots at WHOI.
Here, fabricator Paul Keith talks about how he created a smooth curve in a piece of titanium.
I’m bending a radius on that titanium part. It’s like a weird-looking triangle, six or seven feet long and probably four or five feet wide. I think there was one on either side of the sub, port and starboard. It goes on top of the flotation foam and has long bolts go through it and the foam to keep the foam on. The curve lets it fit over the edge of the foam.
The machine is called a press brake. It bends metal. You put the piece of metal in there and the machine presses down on it, puts a bend in it along a straight line, like folding a piece of paper. But you can’t make a sharp bend on a thick piece of titanium, because it’ll break. If you want a curve, you make multiple small bends close together, so it gives an even sweep, so it’s nice and round.
Then I use that wood template I made that’s the actual shape they wanted. You hold that in there to judge that you’re getting a round shape. As you rock that template back and forth, you can tell if there’s a high spot or it’s not quite bent right.
The secret is to creep up on it slowly. You can’t bend too much, too fast. So you kind of hit it a little bit and get a little bit of a bend. Then you start working it back and forth. It’s like rolling dough. If you try to hurry it and hit it real hard, you’re all done. It’s better to keep ding-ding-ding-ding-ding-ding-ding. It should bend evenly. If it doesn’t, tough luck. You know, there’s no unbending—only bending.
If something turns out wrong, you have to start with a new piece. That didn’t happen with these. Lucky! It depends on the tolerances, a lot of times. I always tell the designers, ‘the bigger the tolerance, the better. If you make it too tight, we might be doing a lot of them.’
I’ve been at WHOI close to 10 years now, as a fabricator and welder, on different projects. I’ve been doing this since I was 21. I like to build things that are one-of-a-kind.
This project has been pretty interesting. What I like is the different personalities. We have every mix of character. Each person adds their little bit. Everybody says a lot about the new technology, but you know, it’s a lot more tricky with the innovative personalities mixed with the technology. Most people wouldn’t realize what it takes to do something like the Alvin project—all the different people that have to work at it. Everybody thinks it’s just somebody with a Ph.D.
Alvin is owned by the U.S. Navy and operated by WHOI. The current upgrade has been funded largely by the National Science Foundation, with support from private donations to WHOI.
From the Series
Related Articles
- The story of a “champion” submersible
- Robots to the Rescue
- Who is Alvin and what are sea trials?
- 7 Places and Things Alvin Can Explore Now
- The story of “Little Alvin” and the lost H-bomb
- Meet the Alvin 6500 Team: Lisa Smith
- Overhaul to take Alvin to greater extremes
- Meet the Alvin 6500 Team: Rose Wall
- Racing an undersea volcano
Featured Researchers
See Also
- Building the Next-Generation Alvin from Oceanus magazine
- Alvin Gets an Interior Re-design from Oceanus magazine
- New Personnel Sphere Passes Pressure Test WHOI News Release
- Human Occupied Vehicle Alvin
- Alvin's Pilots from Oceanus magazine
- National Deep Submergence Facility