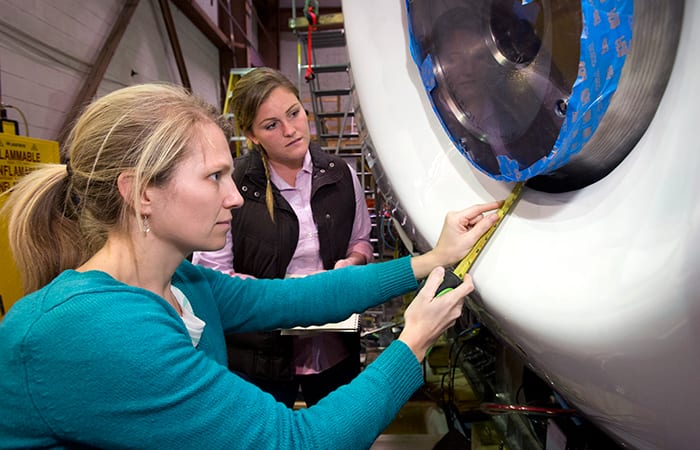
Rebuilding Alvin: Carroll & McCartney
A series on the people who reassembled the iconic sub
From the beginning of 2011 to May 2013, Alvin, the U.S. science community’s only human-occupied submersible dedicated to deep-sea research, underwent a thorough overhaul and upgrade to greatly enhance its capabilities. In the end, the iconic sub was redesigned and rebuilt, piece by piece, by a one-of-a-kind team of engineers, technicians, and pilots at WHOI.
Megan Carroll and Kaitlyn McCartney worked on the foam pieces that provide buoyancy to Alvin and here they describe how the foam was made, fitted, and documented.
Megan: For the new Alvin, we re-used previously existing syntactic foam, but we also needed new foam pieces shaped specifically for this upgrade. I worked on designing the pieces, and also worked with the machine shops that machined raw foam blocks into the final shapes for the new sub.
Once we had final designs for the shapes we needed, we sent drawings to a machine shop, which bonded raw blocks of syntactic foam together and machined them into final shapes.
Kaitlyn: And then we finalized how to attach the foam to the sub’s frame. That’s when I got involved working with Megan, looking at the attachments and brackets.
Megan: When a foam piece comes back from the manufacturers, we check its dimensions. Then you fit it onto where it’s supposed to sit on the vehicle, make sure that there aren’t any interferences and that the clearances you allowed for are there. That’s called “fitting it up” with the vehicle.
These particular blocks—one port and one starboard—are referred to as the “cheek blocks.” We were making sure the opening of the foam over the Alvin’s viewport was pretty well centered, and marking its final location. The cheek blocks fit around the sphere, with an inside curvature around the sphere and an outside curvature from top to bottom and fore to aft, so there are two different profiles to fine-machine.
Kaitlyn: Every piece of foam had its weight taken—in air and ‘wet,’ or in water. We had to prove that the brackets would hold the foam on the vehicle by withstanding stresses caused when they transition from water to air. Every piece of bracketry and long tie rods that tie foam pieces together and to the frame, all had to be individually analyzed.
Megan: … under various operational and emergency conditions.
Kaitlyn: Say if the submarine was transiting along the bottom and unexpectedly impacted something; is that force enough to cause a bracket to fail and release a piece of foam?
Megan: Because the foam is required for the vehicle to re-surface.We analyzed 16 foam pieces, the brackets, the bolt sizes and materials, the shape of the brackets, and the hole locations—things like, ‘What’s the spacing between the hole and the edge of the material? Where might it fail?
Kaitlyn: You know, ‘Will a force take that bolt and rip it through that piece?’ Then we did another analysis for the forces various inserts could withstand before pulling out of the foam. We started the analysis in August, and submitted it initially in December. It ended up just under 200 pages of calculations when printed.
Megan: I’ve been here since fall 1999, and I got involved with the Alvin Upgrade project probably the end of 2009.
Kaitlyn: I’ve been at WHOI since the start of 2011, and was brought into the Alvin project at the end of 2011. I worked on a lot of designs and calculations. It was nice to see the vehicle coming together. It’s cool to see it on the computer screen, eight inches big every day, and then go and see it in person, and it’s like, ‘Wow,’—because you lose the scale sometimes. I know I do.
Alvin is owned by the U.S. Navy and operated by WHOI. The current upgrade has been funded largely by the National Science Foundation, with support from private donations to WHOI.
From the Series
Related Articles
- The story of a “champion” submersible
- Robots to the Rescue
- Who is Alvin and what are sea trials?
- 7 Places and Things Alvin Can Explore Now
- The story of “Little Alvin” and the lost H-bomb
- Meet the Alvin 6500 Team: Lisa Smith
- Overhaul to take Alvin to greater extremes
- Meet the Alvin 6500 Team: Rose Wall
- Racing an undersea volcano
Featured Researchers
See Also
- Building the Next-Generation Alvin from Oceanus magazine
- Alvin Gets an Interior Re-design from Oceanus magazine
- Alvin's Pilots from Oceanus magazine
- New Personnel Sphere Passes Pressure Test WHOI News Release
- National Deep Submergence Facility