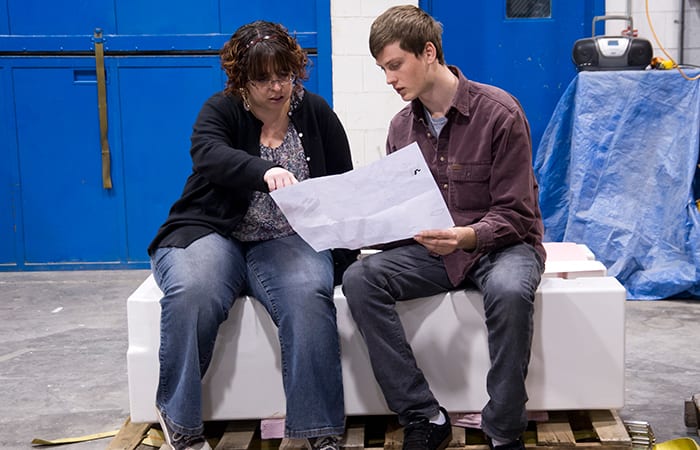
Rebuilding Alvin: Elder and Fournier
A series on the people who reassembled the iconic sub
From the beginning of 2011 to May 2013, Alvin, the U.S. science community’s only human-occupied submersible dedicated to deep-sea research, underwent a thorough overhaul and upgrade to greatly enhance its capabilities. In the end, the iconic sub was redesigned and rebuilt, piece by piece, by a one-of-a-kind team of engineers, technicians, and pilots at WHOI.
Christine Fournier and Fran Elder describe some designing, modeling, and drafting work they did for Alvin, including its rescue buoy.
Fran: We’re sitting on the foam block that is the major piece of Alvin’s rescue buoy. If you’re entangled on the bottom, and you drop the emergency releases, and still can’t get Alvin to float up, you release the rescue buoy, so the ship can find Alvin if it ever got stuck.
Christine: There is acoustic equipment on the buoy that the ship can listen for.
Fran: The buoy is attached to a line and floats up far enough so that the ship can tow a detection instrument by and locate the buoy. Then they would send another vehicle down for the line and pull Alvin up.
Christine: At the back end of the buoy, there’s a bolt. To release it, pilots send an electrical signal to the bolt, and it breaks, which lets one end of the buoy go. At the other end is a bracket, like a little hook, and the buoy’s buoyancy pulls it off that hook.
Fran: I did some of the design work on the brackets. It’s definitely a team effort. A lot of people have worked on this.
Christine: I did drawings for this. We do computer modeling to design components and systems, then put all that information on drawings. Fran worked on them, then I worked on them, and other people. And then Fran refined how everything fit, because we have to make components fit as we go along.
Fran: Like in a car, you have a certain amount of space, and everything has to fit and line up, and you build in tolerances. We were re-using part of the old Alvin frame that was …
Christine: … built by hand!
Fran: It’s definitely a one-off thing, so some trimming is needed. For example, they had to drill a really, really long hole through the buoy—for a tie rod that goes all the way through. And you can model it, and say, ‘This hole’s gonna come out the other end in the perfect spot.’ But when you drill a hole that long, with a really long drill bit, there’s just no way it’s going to be perfect.
So it came out a little to one side, and we had to slot the hole a tiny bit in order to center the brackets, so everything else would work. You know, in the model you can do something that, in the real world, you may or may not be able to.
Christine: I’ve been here four years. I have my associates’ degree in engineering, and a bachelor’s in art history—completely unrelated! I had done administrative and library work, so I’m doing document management, making sure drawings have the right information. But I’ve also been drafting and modeling. Whoever needs me to do stuff, I’ve just been there, doing it.
Fran: I’ve been working with Alvin since January 2012. I got my four-year engineering degree just after I got hired and was promoted to engineer. I was hired for drafting but ended up doing design work. That’s what I like—do something creative, solve some problems. Christine’s got the discipline and organization! I think between the two of us we’ve worked on just about every system on Alvin.
Alvin is owned by the U.S. Navy and operated by WHOI. The current upgrade has been funded largely by the National Science Foundation, with support from private donations to WHOI.
From the Series
Related Articles
- The story of a “champion” submersible
- Robots to the Rescue
- Who is Alvin and what are sea trials?
- 7 Places and Things Alvin Can Explore Now
- The story of “Little Alvin” and the lost H-bomb
- Meet the Alvin 6500 Team: Lisa Smith
- Overhaul to take Alvin to greater extremes
- Meet the Alvin 6500 Team: Rose Wall
- Racing an undersea volcano