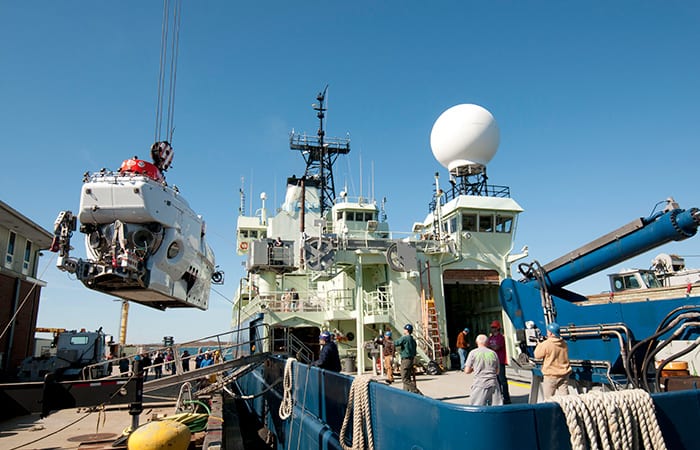
At 50, Alvin Gets an Extreme Makeover
Same name, but dramatically upgraded submersible
Since its birth in 1964, the deep-sea research submersible Alvin has been brought in every few years for overhauls. Most were routine maintenance—the submarine equivalent of a 30,000-mile service on your car.
“You have to take the vehicle completely apart to check the structural integrity of the sphere, frame, and other components,” said Anthony Tarantino, a former Alvin pilot. “But you only make minor changes and usually put it back together, configured in very much the same way.”
Some overhauls were more substantial, incorporating new technology and improvements. Alvin evolved. The original steel personnel sphere was replaced in 1973 with a titanium one that allowed Alvin to reach depths of 4,500 meters (2.8 miles). Along the way, a second manipulator arm and video cameras were added. Thrusters replaced a stern propeller to increase speed and maneuverability. Alvin’s white sail became red-orange to make it easier to spot when it surfaced.
As a result, the original sub that was christened a half-century ago looked very different from the one that investigated impacts from the Deepwater Horizon disaster in the Gulf of Mexico in December 2010. After that mission, Alvin was brought to Woods Hole Oceanographic Institution (WHOI) for a scheduled overhaul.
But this overhaul was nothing like all the rest.
The sub that engineers at WHOI began to disassemble in 2010 bore the same name as the one that was loaded on board the research vessel Atlantis in May 2013. But so does a 2014 Cadillac and the one your grandfather owned.
“This new Alvin has about 70 percent new components,” said Pat Hickey, who headed the Alvin Operations Group during the overhaul project. “We basically redesigned and rebuilt the entire vehicle.”
How that happened is a tale that began in the mid-1990s, when the community of ocean scientists first began contemplating what the future of deep-sea research would look like in the new millennium.
HOVs, ROVs, and AUVs
The notion of a human-occupied deep-sea vehicle, or HOV, first took root at a meeting of 103 scientists in Washington, D.C., in 1956. They had convened to chart a road map to explore the ocean depths, which were virtually unknown at the time. An eloquent argument by WHOI scientist Allyn Vine stirred scientists to recommend building an HOV, which was later named in his honor.
In the late 1990s, scientists once again convened to discuss deep-sea capabilities and assets they sought for the future. “A generation on, it was time to take stock again,” said Chris German, chief scientist from 2006 to 2014 for the National Deep Submergence Facility (NDSF) at WHOI, which operates deep-sea vehicles for the research community.
By this time, Alvin had inspired new generations of deep-sea tethered remotely operated vehicles (ROVs) and free-swimming autonomous underwater vehicles (AUVs). With proponents of all technologies competing for limited funds, a vigorous debate ensued.
In the end, “It’s a little like that game rock, paper, scissors: Each brings something to the table that beats another one,” said Peter Girguis, chair of the DEep Submergence Science Committee (DESSC), the group of scientists that advises the NDSF. Tethers on ROVs provide power but constrain mobility. HOVs and AUVs are free-swimming, but limited by battery power. AUVs cover more ground, but they are also unpiloted and have limited sampling capabilities compared to ROVs and HOVs.
“One of the biggest advantages of a human-occupied vehicle for scientists is having the ability to take in the context of the environment firsthand,” Girguis said. “If you are a deep-sea ecologist, you want to have the best understanding of the organisms’ habitats. You can sample fine-scale attributes of deep-sea communities and simultaneously see the large-scale perspective of where they fit in. You get an instant photomosaic of the big picture.”
In a 1999 report, with the tortured acronym DESCEND (Developing Submergence SCiencE for the Next Decade), a scientific committee recommended pursuing all three technologies, including an HOV that could dive deeper than before. In 2004, a committee convened by the National Academy of Sciences concurred, calling for an “HOV capable of operating at significantly greater depths, if it can be delivered for a relatively small increase in cost and risk.”
“Diving to 4,500 meters, Alvin allowed us to reach 63 percent of the ocean; we wanted to reach 98 percent,” said Dan Fornari, chief scientist for the NDSF from 1993 to 2004. That would require descending to 6,500 meters, or more than 4 miles.
“Alvin’s depth capability was last enhanced in 1973 to 4,500 meters to reach the mid-ocean ridges,” German said, “but it could not reach the deeper abyssal plains around them. And 6,500 meters is the hinge point for subduction zones, where tectonic plates bend into ocean trenches.”
A ‘holier’ sphere
In 2004, scientists at WHOI—Fornari, Bob Detrick, vice president for marine operations, and Barrie Walden, longtime head of the Alvin Operations Group—put in a proposal to the National Science Foundation (NSF) to consider a next-generation vehicle with a new personnel sphere that could not only go deeper, but had other improvements that scientists wanted, including more interior room and more and bigger windows, or viewports.
“Nobody had built a sphere like this in a generation,” German said. “It was seen as a high-risk project. And we said, ‘Oh, by the way, we’d also like to punch more holes in the sphere than we had previously, and we want them to be bigger holes.’
“Alvin was such a pioneer,” German said. “When it was built 50 years ago, nobody knew what there was to see on the seafloor. Engineers said, ‘What’s the maximum visibility we can get with the fewest holes that would least compromise the sphere’s safety?’ ”
The original Alvin ended up with four 5-inch-diameter viewports, one looking forward for the pilot, one for each observer on the port and starboard sides, and one rarely used viewport on the bottom of the sphere. Collectively, this provided the widest possible field of view for the two observers and pilot—but no overlap. “Once Alvin began to make fascinating discoveries on the seafloor, scientists and pilots realized they could never see the same view as one another, at the same time, to discuss what they were looking at,” German said.
Think about that for a minute. Imagine you and your sibling packed in the back seat of your mom’s subcompact car on an all-day road trip. Each of you can see only out of a small window on your side and neither can see what your mom is looking at out the front window.
“Everyone inherited that configuration for a generation,” German said. “But with 50 years’ experience, we asked to add two new forward-looking viewports and make them bigger, so pilots and scientists could work together more efficiently.
“I was pretty sure I was causing our engineers headaches by making that request,” he said. “But this sphere would be the one we would have for the next half-century. We only get to do this once. And these were some of the best engineers on the planet. They’ve got centuries of cumulative experience of how to do these things, so I wasn’t planning to back down in a hurry. Happily, they understood the compelling reasons behind what was being asked of them, and they said, ‘We’ll find a way to put more holes in the sphere and keep it strong enough to dive with humans to 6,500 meters and back.’ ”
In 2004, the NSF agreed to the plan and awarded a $22.91 million contract to build a new vehicle with a new, larger, thicker sphere. In 2005, Southwest Research Institute received the contract to build the new sphere. Two years later, Lockheed Martin won a bid for a preliminary design to build the rest of the sub.
A two-stage plan
Not surprisingly during such a large, long-term project, unanticipated circumstances arose. For example, titanium became the material du jour for golf clubs and tennis rackets, and prices rose substantially, said Susan Humphris, the WHOI scientist in charge of the Alvin upgrade from 2008 to completion. She inherited the project from Detrick when he became director for NSF’s Earth Sciences Division in 2008.
Then another unexpected price hike emerged. Lockheed Martin’s preliminary design came in at more than double the cost that NSF had budgeted.
In another hitch, the plan had also envisioned replacing lead-acid batteries on Alvin with lighter, high-powered lithium batteries that would allow the sub to dive to 6,500 meters. But lithium batteries were showing risks for fires. “It became clear that lithium battery technology was not mature enough to put safely into an HOV,” Humphris said.
At a tense meeting in Washington, D.C., in 2008, the scientific committee overseeing the Alvin upgrade convened to figure out what to do. “Should we forge ahead or abandon the project? We weren’t sure how it would come out,” Girguis said. “We knew we had momentum, and if we didn’t proceed now, there would be no Alvin.”
“We decided that Alvin was a really important national asset for research,” German said. “But we couldn’t move forward in the way NSF had originally envisaged. It was just going to be too expensive, and the technology was not yet there. We had to think carefully about what we were, and weren’t, going to do. We developed a new plan, with a longer-term two-stage approach, still aiming to achieve the same endgame.”
In stage 1, engineers would incorporate the new sphere and several other improvements to return Alvin as soon as possible to service—unable to dive deeper right away, but substantially enhanced. In stage 2, as more funding and battery technology became available, other Alvin systems would be modified to increase the entire sub’s depth capacity to 6,500 meters.
Bringing the project in-house
The intense discussion and change in plan fomented another previously unconsidered option: “We thought we could internalize the project and do it at WHOI,” said Tarantino, who became assistant project manager for the upgrade project in 2007. “We had the engineering expertise in-house. And we had nearly 50 years of experience in Alvin operations. We also knew what the scientific community was going to demand, what they were going to need to be successful. And we believed we knew how to give it to them much better than anyone else. If we could pull it off, in the end, we felt we’d be much more likely to deliver a product that was going to fulfill the needs of the science community and was going to be as safe and reliable as Alvin had been in the past.”
“It’s easy to draw concepts on a piece of paper, but when you’ve physically got to put it on the submarine, it’s something totally different,” said Hickey, the Alvin Group leader. “Engineers might design something into a small location that we knew was buried so deep, we couldn’t actually get at it to repair it if we ever needed to. Or, it was like, ‘How are we going to actually fasten that part you designed to the frame?’ A lot of the things they were designing, we had tried in the past and found didn’t work, or didn’t work as well as the way they were designed to.”
“It was hard to argue that an outside company had a better skill set to build a deep-sea HOV,” German said. “And taking advantage of the engineering expertise at a nonprofit organization might make the project more affordable.”
Managing the matrix
What WHOI didn’t have, unlike most corporations, were well-ingrained structures for project management. Rather, it is more of a matrix organization that “endeavors to fit people into slots where they’re needed, and then move them on to other projects,” said Don Peters, a WHOI senior engineer. “WHOI has various projects funded at any time that have needs for various types of engineers—mechanical, electrical, software. You maintain staff capability by cleverly moving them among places where the work is. People combine several funded projects to keep their dance cards full.”
The downside is that, to make ends meet, WHOI engineers have several projects with several masters on their dance cards. “The Alvin project was not the only game in town,” Hickey said, “and it turned into a much larger enterprise than we anticipated.”
“We didn’t have a dedicated staff or formal means to manage engineering resources,” Tarantino said. “We had a year of growing pains. But early on, we assembled teams to figure out key enabling technologies, and we picked key people to fill key roles.
“We brought Barrie Walden out of retirement as the technical director, or chief engineer,” he said. Walden also took charge of acquiring new syntactic foam to get more buoyancy without more weight.
Peters, a mechanical engineer, led a team to modify the sub’s old titanium frame (re-used to save costs), to calculate and accommodate the new weight and balance of the sub, and to design, fabricate, and conduct structural analyses for new brackets, mounts, and connections for new components.
“Lane Abrams was the lead electrical guy who designed the architecture for the new electronics,” Tarantino said. “Jon Howland was the lead software engineer, working on new command-and-control and data-logging systems for the sub. There was me, as assistant project manager. Pat [Hickey] was the operations liaison for the Alvin Group. Rick Chandler was our business manager. Over the course of the project, Don left to go to another project, but later returned as chief engineer. Barrie Walden really did retire, a second time, and we replaced him with Rod Catanach. Kurt Uetz was hired as project manager in 2010. We pushed on.”
Certifying safety standards
WHOI also did not have built-in systems to accommodate the voluminous documentation and certification required by funding agencies, the Navy, and other officials. Former Alvin pilot Jeff McDonald took on that mammoth, unrelenting job—one that expanded exponentially because of another unexpected complication.
Like most ships, Alvin must be designed, built, tested, maintained, operated, and certified under safety standards set by a designated organization. In the past, that had been the Naval Sea Systems Command, or NAVSEA, but the Navy did not express interest in playing a role in certifying the new Alvin. So WHOI engineers proceeded, complying with certification standards set by another organization, the American Bureau of Shipping, or ABS.
Two years into the process, the Navy decided it wanted to certify Alvin under NAVSEA rules. Rather than start the certification process at the beginning again, WHOI engineers thought they could build on what they had already done for ABS.
“One would think that there would be a lot of overlap between the two sets of rules,” Tarantino said, “and where they don’t overlap, you might say, ‘We’ll pick the more difficult rule, and that will satisfy both.’ We worked very hard to satisfy both or to get the two organizations to collaborate and agree to some common standard.”
But irreconcilable differences arose, and the project had to comply completely with NAVSEA. The unanticipated change cost time and money.
The finish line
Meanwhile, the sphere project began with three massive titanium ingots totaling 41,000 pounds in a mill in Pennsylvania. The 11,000-pound sphere that arrived at WHOI in June 2012 was as spherical and flawless as humanly possible to avoid defects that could compromise its integrity under intense pressure. It was thicker (2.8 versus the old sphere’s 2 inches) to withstand depths up to 6,500 meters.
The new sphere was wider, with a 6.5- versus 6-foot diameter. It provided 18 percent more interior room to include creature comforts such as padded benches for observers to sit or lie on, instead of having to scrunch with legs intertwined on the sparse floor of the sphere.
Importantly, the new sphere had all five viewports that scientists had asked for, including three forward-looking ones with overlapping fields of view for pilots and scientists. The forward-looking viewports were also larger than before: 7 rather than 5 inches in diameter. And it had two more holes near the nape of the sphere for new penetrators, the connectors through which all power, commands, and data are transmitted between the sphere’s interior and electronics in pressure housings outside. The penetrators, for the first time on Alvin, were equipped with fiber-optic cables that dramatically increased power and bandwidth, enabling enhanced capabilities including a suite of high-definition video cameras.
Soon after the sphere arrived at WHOI in June 2012, it was installed on Alvin’s retrofitted frame. Over the next year, engineers and technicians swarmed to install and test the remaining components and reassemble the new sub.
The final price tag was $41 million, of which $11.8 million paid for the sphere. NSF paid $36 million. Private WHOI funds paid for the rest.
In May 2013, Alvin was loaded back onto Atlantis. In November 2013, the Alvin Operations Group, along with Navy observers, conducted certification dives off San Diego, Calif. In January 2014, the Navy certified the sub to resume operations. And in March 2014, about 10,000 pounds heavier and loaded with enhanced capabilities, Alvin returned to service, right where it left off, in the Gulf of Mexico.
“So many people participated in building this new vehicle—more than 100 at WHOI alone,” said Humphris. “It’s a testament to their broad range of skills and their dedication that they were able to come together to create such an amazing vehicle.”
From the Series
Slideshow
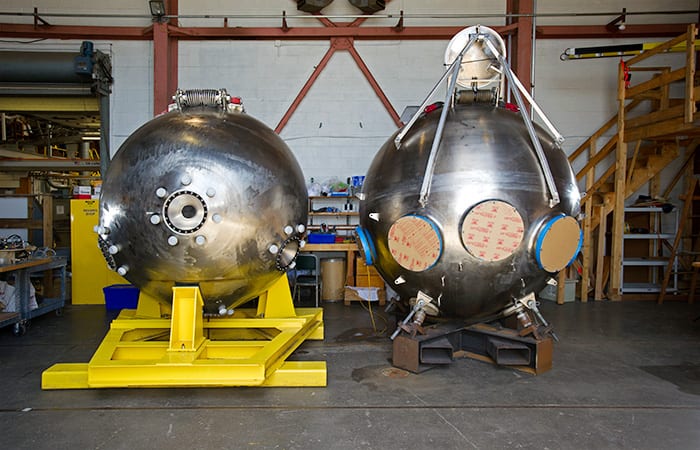
Slideshow
- Alvin's old sphere (left) had only one forward-looking viewport for the pilot, and so scientists looking out the port and starboard viewports could not simultaneously see what the pilots was looking at. The new sphere has three forward-looking viewports, with overlapping field of views for pilots and scientists. (Matthew G. Barton/Woods Hole Oceanographic Institution)
- Piece by piece, engineers and technicians such as Vic Miller designed, fabricated, and assembled the new Alvin. (Tom Kleindinst/Woods Hole Oceanographic Institution)
- A portion of the more than 100 WHOI engineers, technicians, pilots, scientists, administrators, and others, who mustered to build the new Alvin. (Tom Kleindinst/Woods Hole Oceanographic Institution)
- WHOI engineers, including (from left) Anthony Tarantino, Bob McCabe, and Rod Catanach, devoted years to building the new sub. (Tom Kleindinst/Woods Hole Oceanographic Institution)
- Susan Humphris was the WHOI scientist in charge of the Alvin upgrade project. (Tom Kleindinst/Woods Hole Oceanographic Institution)
- "This new Alvin has about 70 percent new components," said Pat Hickey, Alvin pilot and former head of the Alvin Operations Group at WHOI. "We bascially redesigned and rebuil the entire sub." (Tom Kleindinst/Woods Hole Oceanographic Institution)
Related Articles
- The story of a “champion” submersible
- Robots to the Rescue
- Who is Alvin and what are sea trials?
- 7 Places and Things Alvin Can Explore Now
- The story of “Little Alvin” and the lost H-bomb
- Meet the Alvin 6500 Team: Lisa Smith
- Overhaul to take Alvin to greater extremes
- Meet the Alvin 6500 Team: Rose Wall
- Racing an undersea volcano
Featured Researchers
See Also
- Trailblazer in the Ocean Oceanus magazine
- The Once & Future Alvin
- Bringing Alvin Back on Board
- Ready, Set, Dive
- Happy 50th Birthday, Alvin
- Happy 50th Birthday, Alvin website
- Newly Upgraded Alvin Submarine Passes Scientific Sea Trials WHOI media release
- Alvin Science Verification Cruise WHOI Blogs & Expeditions
- Alvin Upgrade
- Frequently Asked Questions about Alvin WHOI Ocean Instruments
- National Deep Submergence Facility at WHOI
- Alvin's Pilots Oceanus magazine