A new way of “seeing” offshore wind power cables
Researchers test ocean robots to make subsea cable surveys faster and cheaper
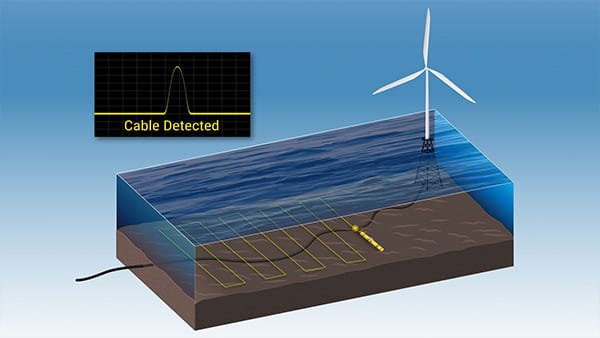
Estimated reading time: 6 minutes
In 2016, when an oil tanker off the British mainland came upon a patch of stormy weather near the Channel Islands, it dropped anchor to wait things out. Moments later, internet speeds on the UK island of Jersey plummeted.
It turns out, as the anchor hit bottom, it snagged a few network cables on the seafloor and severed them, leaving internet users across the island temporarily out of access.
Autonomous underwater vehicles (AUVs)—a staple of oceanographic research—can perform subsea cable surveys faster and more economically than using ships with towed instruments. (Animation by Natalie Reiner and Craig LaPlante, Woods Hole Oceanographic Institution)
In 2016, when an oil tanker off the British mainland came upon a patch of stormy weather near the Channel Islands, it dropped anchor to wait things out. Moments later, internet speeds on the UK island of Jersey plummeted.
It turns out, as the anchor hit bottom, it snagged a few network cables on the seafloor and severed them, leaving internet users across the island temporarily out of access.
Internet cables aren’t the only form of underwater wiring vulnerable to snags on the seafloor. High voltage cables supplying power from the mainland to offshore wind farms are also easy targets if they’re not adequately protected. These black, rubber-coated cables are not the most glamorous components of offshore wind—but they’re critical veins of power that wind operators, developers, and coastal communities rely on to keep this brand new source of clean energy in the U.S. going.
“Most people focus on the spinning blades of turbines to ensure that an offshore wind energy project will be successful, but the subsea cables that bring that power to land are equally as important,” said Anthony Kirincich, a physical oceanographer at WHOI. “Power can be cut by cable damage from ship anchors, fishing trawlers, or storms. So, these cables need to be routinely surveyed and maintained to ensure a project will continue to provide power to the grid, and revenue to the operators.”
The need for speed
Subsea cables have traditionally been inspected using ships with towed instruments such as sub-bottom profilers, side-scan sonar systems, and cameras. They check to see if cables are buried at the right depth, if they are in the correct position, or if they are exposed in way where they can be easily snagged by anchors or trawl nets.
The ship-based approach works, but the use of ships can be extremely expensive and time consuming. Kirincich says that autonomous underwater vehicles (AUVs)—a staple of oceanographic research—could be used in place of large, expensive ships to perform cable surveys much more quickly and at far lower costs.
“AUVs can cut down on ship costs and weather delays, while reducing the time required to gather the data operators need to assess their underwater infrastructure,” he said.
WHOI researchers deployed a REMUS 600 AUV to survey a subsea cable system in Buzzards Bay, Mass. The vehicle uses a propeller and fins for steering and diving, and relies on an internal navigation system to independently survey swaths of the ocean. (Photo by Evan Lubofsky, Woods Hole Oceanographic Institution)
Coming to a seafloor near you
Until recently, there hasn’t been a huge need for ship-based surveys in the U.S. offshore wind sector, simply due to the fact that only one offshore facility—the Block Island wind farm off the Rhode Island coast—is currently in operation. But that’s about to change. New offshore developments are on the horizon, being driven in part by an energy bill passed in Massachusetts—An Act to Promote Energy Diversity—which requires state utilities to draw on at least 1,600 megawatts of offshore wind energy by 2027. Vineyard Wind, a developer in New Bedford, Mass., nabbed the state’s first offshore wind contract and is planning to build an 800-megawatt facility consisting of 100 turbines in federal waters south of Martha’s Vineyard. And other firms are lining up sites and operating contracts for areas up and down the east coast.
A new submarine cable set to run along the East African coast and into the Red Sea is being planned for launch, which will help boost internet speed and mobile communication in Tanzania. (©clubofmozambique.com)
More wind farms mean more subsea cables. So WHOI researchers, eager to share their own best practices and technical know-how with the offshore wind sector, recently field tested a REMUS (Remote Environmental Monitoring UnitS) AUV to see how it performed during a mock cable survey. Designed by WHOI’s Oceanographic Systems Lab, REMUS is a torpedo-shaped ocean robot that operates autonomously and is programmed and monitored via laptop. The vehicle uses a propeller and fins for steering and diving, and relies on an internal navigation system to independently survey swaths of the ocean.
“REMUS is one of the most capable AUVs available today for surveying the sea floor,” said WHOI engineer Robin Littlefield. “It serves as a flexible platform for various types of underwater sensors. In that sense, it’s a workhorse that we sometimes liken to a pickup truck that you can equip with just about anything.”
On a mission
WHOI researchers deployed the AUV to survey a subsea cable system in Buzzards Bay that links Martha’s Vineyard to grid power from the mainland. For this particular field test, Littlefield and his team modified a standard REMUS 600 with magnetometer sensors—one built into the nose of the vehicle and another, smaller one mounted on top—to track the underwater cable. The AUV was transported offshore with a small support boat, and surveyed a one-kilometer section of cable using a lawnmower-like pattern a few meters above the seabed.
(Video by Craig LaPlante, Woods Hole Oceanographic Institution)
Each time the vehicle transected the cable, the magnetometers picked up the electromagnetic field emanating from it and recorded a “spike.” A side-scan sonar system, also mounted onto the AUV, was used to image and map the seafloor around the cable in order to collect detailed information such as the presence of gaps in the sediment protecting the cable.
“We were able to collect side-scan, sub-bottom, and magnetometer data from a single REMUS vehicle in a matter of hours,” said Littlefield. “It may have taken days with a ship.”
Use of the support boat helped streamline the field testing, but Littlefield says the AUV can be run directly from shore in the future to make the process even more efficient.
Beyond proof-of-concept
The next step will be analyzing the recorded data, a process that will involve visually overlaying the side-scan sonar and magnetometer measurements to make sure they correlate. The researchers will also compare electromagnetic signal measurements from the larger, onboard magnetometer sensors to that of the smaller, top-mounted sensor.
“Once we’re able to ground-truth the performance of the smaller magnetometer, we’ll look towards developing a low-cost sensor suite based on that technology that can become a standard on REMUS vehicles,” said Littlefield. “This will ultimately make it even more economical for the offshore wind industry to collect the information they need to assess the status of their infrastructure.”
Kirincich agrees, and says that in general, AUVs are a good example of a field-proven ocean technology that could and should be leveraged for U.S. offshore wind projects.
"As oceanographers, we have a role to play in transferring new technology solutions to the offshore wind sector," he said. "REMUS is one tool we rely on heavily that could be transitioned into the industry for its benefit."
This work was funded by a joint partnership between WHOI and the Massachusetts Clean Energy Center. The Woods Hole Oceanographic Institution is a private, non-profit organization on Cape Cod, Mass., dedicated to marine research, engineering, and higher education. Established in 1930 on a recommendation from the National Academy of Sciences, its primary mission is to understand the ocean and its interaction with the Earth as a whole, and to communicate a basic understanding of the ocean’s role in the changing global environment. For more information, please visit www.whoi.edu.