Marine
Adhesives
Student
report of test results: epoxies that may be applied and cured
under seawater
Report
prepared by Massachusetts Maritime Academy cadets
Foley,
Holcroft, Maguire, McCormick, McQueen, Pike, and Sunde
Strength
of materials tests by Prof. Ucci's
Student
engineers at Bristol Community College
curriculum
development
by
Enid
Sichel, Ph. D.
Massachusetts
Maritime Academy
101
Academy Drive
Buzzards
Bay, MA 02532
participating
institutions:
Massachusetts
Maritime Academy
Woods
Hole Oceanographic Institution
Bristol
Community College
Upper
Cape Cod Regional Technical School
Supported
in part by the National Science Foundation under grant #DUE-0101632
Maurice
A. Tivey and Enid K. Sichel, co-PI's
December
2001
Table
of Contents
1. Introduction:
the charge to the engineers
2. Strength
of materials data: metal and wood fixtures, 5 epoxies tested
under water
3. Other
adhesives tested, adhesion to rocks under water
4. Inventions
of adhesive applicators for use underwater
5. Unanswered
puzzles, questions, and opportunities
6. Conclusions
and recommendations
7. List
of project participants; acknowledgments
8. Appendix
I: sample ID codes
Appendix
II: list of adhesives
Appendix
III: strength of life tested PSI-326
1.
Introduction: the charge to the engineers
Development
of marine adhesives and markers for submersible research vessel
ALVIN: background
Students
prepared and tested marine adhesives and developed an applicator
for undersea use. The Woods Hole Oceanographic Institution
would like to develop an underwater marking instrument, paint
applicator, or adhesive applicator which could be operated
by the grappling arm of the submersible vessel ALVIN. When
ALVIN is on an undersea geophysics mission, there is need
for a method for making markings or attaching tags to rocks
of geophysical interest. The U.S. Navy has identified a list
of off-the-shelf materials that are candidates for underwater
adhesives.
Three
student teams participated in the project. The Mass. Maritime
Academy students were the project engineers. Students from
the Upper Cape Cod Regional Technical School were the technicians,
working under the guidance of Dr. Sichel and the MMA students.
Students at Bristol Community College (BCC) enrolled in a
course on strength of materials played the role of a testing
laboratory.
The
lab portion of the course involved preparing and life-testing
the adhesives. The samples were deployed off the MMA dock,
and observed weekly for life-testing. A paint/adhesive applicator
was designed and built.
What was
our mission?
Our mission
was to experiment and quantifiably test several marine adhesives
to see if one could work at the bottom of the ocean. The requirements
are: to cure in a reasonable time (minutes) and at a temperature
near 3°C.
Why was
this mission undertaken?
The selected
adhesive would assist the submersible ALVIN in marking evolving
geologic forms and to help in the study of the magnetic properties
of the sea floor. The US Navy also has an interest in underwater
technology related to adhesives for various applications.
How we
did our research:
To examine
the possibilities of each adhesive, we developed a series
of tests with a variety of materials. We used test fixtures
of aluminum at varying thickness, mild carbon steel, stainless
steel, and oak wood. We applied the various adhesives on a
predetermined area of the fixtures and allowed them to cure
in air, in refrigerated conditions, and in sea conditions
hanging from our M.M.A. dock. This process gave us four variables:
first, the mixing of epoxy in air; second, the mixing underwater;
third, the application in air; fourth, the application underwater.
After
an adhesive went through these tests, we tried bonding metal,
glass, and plastic to rock surfaces underwater. We used both
scrubbed gravel from the Cape Cod Canal and actual volcanic
rocks from the bottom of the sea, which previous ALVIN missions
brought back.
We used
several adhesives, Epoxo88, Epoxy 10-3070, Biofix 911, Repairitquik,
Fastweld 10, and Smart Glue. Smart Glue had the most promising
results.
A drawing
of a test fixture for tension mode tests of an epoxy bond
is shown in the figure below.
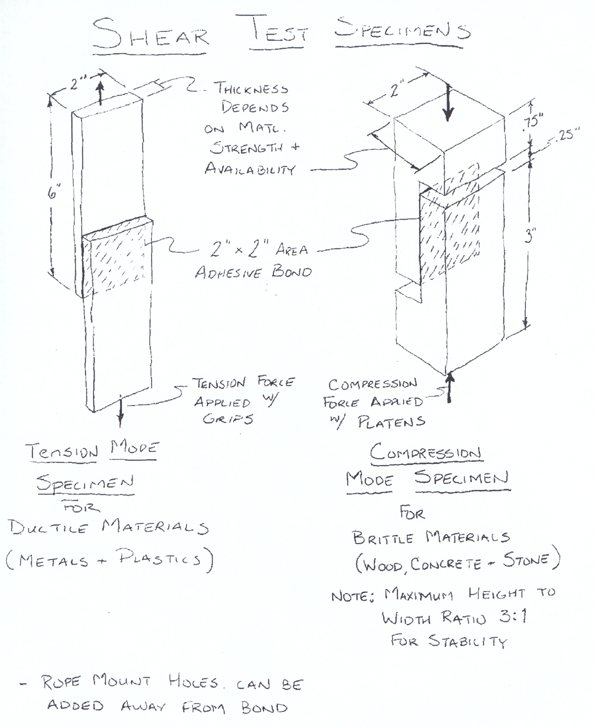
2.
Strength of materials data: metal and wood fixtures, 5 epoxies
tested under water, plus controls
Samples
air cured form the control group. All metal samples were degreased
with mesh soap pads in hot water, dried, and then coated with
epoxy.
Samples
designated REF were prepared by applying the adhesive under
sea water in trays on the lab bench and then moving the trays
of samples in seawater to a refrigerator where they were stored
for 37 days from Sept. 18, 2001 to Oct. 25, 2001 at a temperature
of 44° F. The mixing of the two-part epoxies was done
in air.
Samples
designated SEA were prepared by applying the adhesive under
sea water on the lab bench and then moving the wet samples
to a wire cage and immediately submerging them in seawater
outside, attached to the campus dock. The Bio-Fix 911 samples
were left for 42 days from Sept. 25, 2001 at an ambient sea
temperature of ~19° C and they were harvested on Nov.
6, 2001 at an ambient sea temperature of 13° C. The samples
were kept wet until the time of the strength tests. The samples
of Repairitquik, 10-3070, Fastweld 10, and Epoxo-88 were deployed
for 55 days from Sept. 25, 2001 when the ambient sea temperature
was ~19° C to Nov. 19, 2001 when the ambient sea temperature
was 10° C.
Samples
of PSI-326 (Smart Glue) were tested by mixing the two components
in air on the lab bench. The epoxy was applied under seawater
and the life testing was done under seawater off the campus
dock for 19 days from October 18, 2001 when the sea temperature
was 13° C to November 6, 2001 when the sea temperature
also measured 13° C on the day of harvest. All temperature
measurements were done at mid-day. The samples were suspended
at a depth of about 1 meter below the surface. During the
tests of PSI-326, it was discovered that the two components
could be mixed under seawater, as well as applied under seawater.
The adhesive applicators invented by the students take advantage
of the ability to mix PSI-326 under water.
We note
that there is no strong pattern of test results that depend
on the fixture material. The peel strength was negligible.
Our results suggest that more attention must be paid to the
uniformity of the epoxy film and a greater film thickness
would be beneficial. The most noteworthy result is that
several adhesives that were applied under seawater formed
bonds that survived life tests. The experimental data
are found in Appendix I.
3.
Other adhesives tested, adhesion to rocks under water
PSI-326,
otherwise known as "Smart Glue", was the best adhesive. It
is available in bulk and also in a one shot applicator. In
bulk, it is sold as part A (resin) and part B (hardener).
The mixing reaction of the PSI-326 is exothermic and the manufacture,
Polymeric Systems Inc., recommends limiting the mix to one
teaspoon. By adding glitter powder to the mix, the epoxy can
be used as a marker. The best way to apply it is with a Q-tip
or wooden stick. We found that we could bond etched glass,
smooth glass, plastic tabs and nail heads to the sea rocks.
However, the curing in chilled seawater was not optimal. Out
of the other main adhesives tested, none of them except for
the Smart Glue adhered to the sea rocks! The other adhesives
were: Sta- Dri Hydraulic Cement, PSI-326, Clear RTV Silicone
and Testco Paint Pen for marking. Hydraulic Cement did
bond to rocks underwater, but not to plastic or glass. It
is sold commercially to be used to stop water leaks in concrete
foundations. We found that the cure time was too long to be
practical for ALVIN use. Hydraulic cement came in powder form
and was mixed with seawater to form a putty substance. We
had expected good results with Clear RTV Silicone. Dr. Pocius
of the 3M company believed it would be the best adhesive due
to the fact it was permeable and was able to eliminate the
film of water that was between the surface of the rock and
the adhesive. We expected that the boundary layer of water
would percolate through the adhesive, leaving nothing between
the rock and RTV Silicone. This was proved to be false, however,
because the surrounding water would not allow the boundary
layer to escape. Bonding to a wet surface with RTV Silicone
probably only works in air. The Smart Glue was the better
bond to the submerged rocks.
4.
Inventions of adhesive applicators for use underwater
The best adhesive is nothing without an applicator. This is
why we have tried to develop one that will fit many criteria.
The device would have to be reliable, so a simple design is
an important aspect. As you can see in the diagram below,
this applicator has no moving parts, and few individual pieces.
It is made up of a single aluminum plate along with two sponges,
and a triangular aluminum handle attached to it. These materials,
along with being simple, are also durable and will withstand
temperature changes.
One other
consideration is that human hands will not be operating this
applicator. We had to come up with something that could be
operated robotically, using three fingers, and one arm of
limited movement. This is of course referring to the mechanical
arm of the submersible research vessel ALVIN. This applicator
takes advantage of ALVIN’s ability to spin its three-fingered
hand. Once holding the applicator, all the controller has
to do is press it against the surface to be adhered to and
spin. This is why the applicator’s pyramid shaped handle is
utilized, taking advantage of its three vertical surfaces
to grasp onto.
In addition
to being simple, durable, and able to be manipulated by ALVIN,
this applicator is also disposable. For this reason it can
be left on the bottom of the ocean at no big loss, and is
no threat to the environment. A CAD drawing of the applicator
and a photograph of the prototype sponge applicator is shown
below.
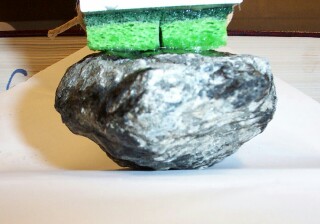
The
second type of applicator, shown below, consists of two segments.
Two corners of a plastic bag ("Baggie") are used, one corner
with the resin, the other corner with the hardener. The ends
of the Baggies are tied off with some twine. The Baggies are
completely filled with one part in each of the corners. The
Baggies are filled so no air bubbles will be present, which
would compress because of the extreme pressure of the ocean
at the depths that ALVIN will be working in. The Baggies are
glued onto a hard rubber stopper. The rubber stopper is made
out of material similar to a hockey puck. On the other side
of the stopper there is a tee handle that ALVIN will be able
to pick up with his robotic arm. ALVIN uses tools that have
a tee handle built into them.
When
ALVIN is ready to use the applicator, he will pick it up from
his basket with his manipulator hand. While holding on by
the tee handle, ALVIN will squish the Baggies and stopper
against the rocks and rotate the stopper over 360 degrees,
mixing both parts of the epoxy and applying it to the rock
to be marked. 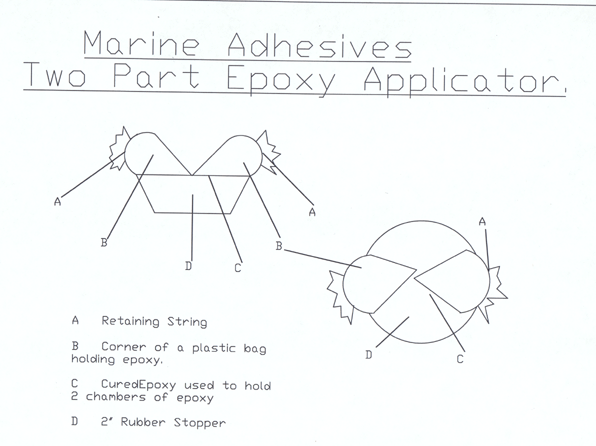
5.
Unanswered puzzles, questions, and opportunities
In the
course of the experiments we noticed that the first five epoxies
tested would adhere to the metals as expected but would not
adhere to rocks, either volcanic or granite. Dr. Pocius shed
some light on this subject. One suggestion was that a weak
boundary layer was created. That is to say that when the epoxy
was applied underwater with no clamping pressure, a layer
of water could have been trapped between the epoxy and the
rock. This boundary could prevent the epoxy from fully adhering
to the rock. Another suggestion of Dr. Pocius was the solubility
parameters of the adhesive. Adhesives are attracted to like
substances. So trying to bond a piece of glass to a rock,
we might find that the adhesive sticks to one but not the
other. A choice for adhering two items with mutual solubility
would have the best results. The metal strips and oak wood
would work because at the time of application, the slabs were
squeezed together pushing out the water that would leave a
boundary layer. The slabs were also joined together with like
substances (wood to wood and metal to metal) that would resolve
the problem of mutual solubility.
Another
suggestion of Dr. Pocius was to use an RTV silicone. The reason
for this suggestion was that the RTV silicone allows water
to percolate through, displacing the weak boundary layer.
However, RTV silicone proved unsuccessful. The cold water
may have slowed down the cure time for the silicone (taking
longer to harden or even by not allowing the silicone to harden
at all). We came across this problem during one experiment
using the RTV silicone by submerging the silicone cartridge
into the cold water to simulate the decent of ALVIN into the
depths and then applying it to the samples of rock, glass,
and various other materials. We let the samples cure and checked
the next week to see the progress. We found that the silicone
did not cure. The RTV silicone allows water to percolate through,
promoting curing when the wet surface is cured in air. When
fully surrounded by water, the silicone may not be able to
keep up with the amount of surrounding water and, therefore,
still allowing a weak boundary layer of water to exist.
The epoxies
may be used in other applications such as on seashells in
aquaculture. Seed shells may be affixed to a wire to start
a colony. This could be accomplished by taking a closer look
at the surface structure of the seashells. This may reveal
how well the epoxies will adhere. A rough surface structure
would be better for the application of epoxies, creating more
surface area for the adhesive to grip. Surface preparation
is a critical part of the application of epoxies. Creating
a surface that is rough for the epoxy to grip but not so rough
that the epoxy can’t adhere to the entire surface or trap
either water or air in the surface grooves. At a microscopic
level, a rock may have a smooth surface and be hard for an
epoxy to adhere to.
During
the course of the semester, we tried several pre-manufactured
applicators and also made our own applicators. We invented
the applicators through a process of brainstorming and trial
and error. Some pre-manufactured applicators may not be available
empty, not allowing us to add the epoxy we find best suited
for the task at hand. Thanks to Mr. Whalen, we know about
a two-chambered applicator that is manufactured
by the 3M Corporation. However, the tubes would have to be
filled by us, with no air bubbles. Our best applicator designs
were the double bag and the sponge type applicator
The best
candidate for epoxies was found to be Smart Glue. We are not
sure why this would be. Upon closer investigation of the Material
Safety Data Sheet (MSDS), we found several chemicals to be
the same in all of the epoxies we tested. When we looked at
Smart Glue we found one ingredient, which was declared a "trade
secret", and therefore the company would not disclose
that information we were curious about.
Shown
below is a photograph of a commercially available pre-loaded
epoxy applicator with a two-chamber barrel for the resin and
the hardener and a set of baffles in the nozzle to mix the
components.
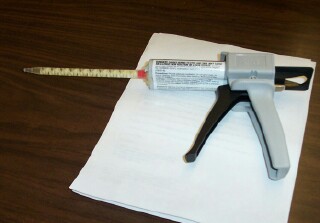
6.
Conclusions and recommendations
Over
the past semester, we have worked with numerous glues and
epoxies. They all have their strong points: some stick better,
apply easier, or wear longer. Finding the right combination
was the key. In the end, Polymeric Systems PSI-326 (Smart
Glue) proved to be the best choice for deep submergence work.
To apply it underwater, new devices needed to be developed
and tested. Two devices, an applicator using sponges, and
another using Baggies of solution A and solution B, were constructed
and tested. A
commercial
applicator gun designed by the 3M company is also on the market.
7.
List of project participants; acknowledgments
Volunteer
students from the Upper Cape Cod Regional Technical School:
Ann
Bodio
Christopher
Francis
Ashley
Lafleur
David
Landolfi
Mark
Mancini
Christopher
Marconi
Mike
Mcgonagle
Ryan
Murphy
Sean
O’ Brien
Emily
Russell
David
Smith
Adam
Thomas
Matthew
Turner
Sarah
Walsh
Jessica
West
Mandy
Westgate
S Chris
Young
Prof.
Ucci’ s Engineering class ETK59 class at Bristol Community
College:
James
Barbaria
Inigo
Loyola
Paulo
Medeiros
Taylor
Michaud
Brian
St. Rock
Channy
Sypaseut
Paul
Ventura
Steven
Wheeler.
Cadets
in Prof. Sichel’s Marine Adhesives class at the Massachusetts
Maritime Academy:
Thomas
Foley
Richard
Holcroft
Tim
Maguire
Brian
McCormick
Timothy
McQueen
Jonah
Pike
Erik
Sunde
We
wish to acknowledge the guests that devoted time out of their
busy schedules to help make some sense out of what we found.
Dr. Maurice Tivey and Mr. Dudley Foster from the Woods Hole
Oceanographic
Institution; Dr. Alphonsus Pocius from the 3M Company; and
Chief Engineer Mark Whalen from Sippican, Inc.
This
project is funded in part by the National Science Foundation.
8.
Appendix I
Epoxy
codes
88
= Epoxo 88 by Fasco Unlimited of Hialeah
911
= Bio-Fix 911 by Progressive Products, Inc.
RIQ
= Repairitquik by Polymeric Systems, Inc.
FW
= Fastweld 10 by CIBA -Geigy Corp.
3070
= Epoxy 10-3070 by Epoxies, Etc.
Date
codes
010913
= Sept. 13, 2001, etc.
Cure
codes
C
or AIR = air cure control samples
REF
= applied in seawater and cured in a lab refrigerator in seawater
SEA
= applied in seawater and cured in seawater off the campus
dock
Fixture
codes
AL
= aluminum shim stock
AH
= heavy aluminum stock
SS
= stainless steel
CS
= mild carbon steel
Appendix
II: list of adhesives
- Fastweld
10 (Ciba-Geigy Corp., 4917 Dawn Ave., East Lansing, MI 48823)
- Epoxo
88 (Fasco Unlimited of Hialeah, Inc., 7735 West 20th Ave.,
Hialeah, FL 33014-3227)
- Bio-Fix
911 (Progressive Epoxy)
- Epoxy
10-3070 (Epoxies, Etc., 21 Starline Way, Cranston, RI 02921)
- FastSteel
and Repairitquik (Polymeric Systems, 723 Wheatland St.,
Phoenixville PA 19460-3394)
- PC-11
(Protective Coatings Co.)
- ACE
10232, store brand (Ace Hardware Stores) Water-proof epoxy
putty
- Smart
GlueR When sold in bulk, product name is PSI-326.
(Polymeric Systems)
- Sta-Dri
hydraulic cement (Sta-Dri Co.)
- Permatex
Black Silicone Adhesive/Sealant (Permatex, Inc. product
#81158)
- Clear
RTV silicone (Permatex, Inc. product #66B)
- BoatLife
Calk (sic) (Life Industries Corp., Charleston SC, product
#1030)
- Testco
paint pen for marking (Testors Co. product #2503C)
Appendix
III: strength test results for PSI-326
|